Custom parts machining is a specialized service that provides precision solutions for businesses and individuals with unique project needs. This process involves creating custom-made parts and components from a variety of materials, including metals, plastics, and wood, to meet specific requirements and specifications. Custom parts machining is essential for industries such as aerospace, automotive, medical, and consumer products, where precision and accuracy are crucial.
The Importance of Precision in Custom Parts Machining
Precision is the hallmark of custom parts machining, as it ensures that the final product meets the desired specifications and performance standards. In many industries, precision is not just a requirement, but a necessity. For instance, in the aerospace industry, precision-machined parts are critical for ensuring the safety and reliability of aircraft and spacecraft. Similarly, in the medical industry, precision-machined components are used in life-saving devices, such as implants and surgical instruments.
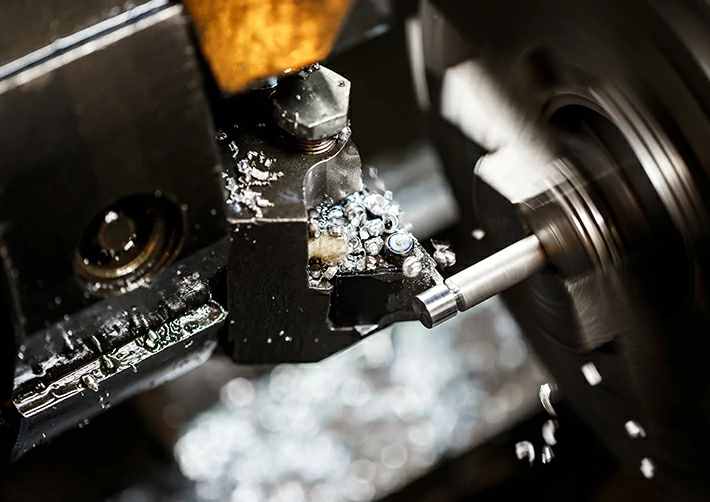
Technologies and Techniques Used in Custom Parts Machining
Custom parts machining employs a range of technologies and techniques to create precision parts and components. Computer numerical control (CNC) machining is a widely used technique that utilizes computer-controlled machines to precision-cut and shape materials into complex geometries and designs. Other techniques, such as 3D printing, wire electrical discharge machining (EDM), and manual machining, are also used to create custom parts with unique features and specifications.
Benefits of Custom Parts Machining
Custom parts machining offers numerous benefits to businesses and individuals seeking precision solutions for their project needs. One of the primary benefits is the ability to create complex geometries and designs that would be impossible to produce using traditional machining techniques. Custom parts machining also provides a high degree of accuracy and precision, ensuring that the final product meets the desired specifications and performance standards. Additionally, custom parts machining allows for rapid prototyping and production, reducing the time-to-market and increasing the chances of success.
Applications of Custom Parts Machining
Custom parts machining has a wide range of applications across various industries, including aerospace, automotive, medical, and consumer products. In the aerospace industry, custom parts machining is used to create complex aircraft components, such as engine parts and satellite components. In the automotive industry, custom parts machining is used to create precision components, such as engine parts, dashboard trim, and exterior body panels. In the medical industry, custom parts machining is used to develop innovative medical devices, such as implants, surgical instruments, and diagnostic equipment.
Material Options for Custom Parts Machining
Custom parts machining can work with a variety of materials, including metals, plastics, and wood. Metals, such as aluminum, stainless steel, and titanium, are commonly used in aerospace and medical applications, where strength and durability are critical. Plastics, such as polycarbonate and ABS, are used in consumer products and medical devices, where flexibility and impact resistance are required. Wood is also used in custom parts machining, particularly in the furniture and construction industries, where aesthetics and durability are important.

Choosing the Right Custom Parts Machining Service Provider
When selecting a custom parts machining service provider, businesses and individuals should consider several factors, including expertise, equipment, and customer service. Expertise is crucial, as it ensures that the provider has the necessary knowledge and skills to create precision parts and components. Equipment is also essential, as it determines the provider’s ability to produce complex geometries and designs. Customer service is vital, as it ensures that the provider is responsive to the client’s needs and can deliver the final product on time and within budget.
Conclusion
Custom parts machining is a specialized service that provides precision solutions for businesses and individuals with unique project needs. By utilizing advanced technologies and techniques, custom parts machining provides a high degree of accuracy and precision, ensuring that the final product meets the desired specifications and performance standards. Whether you are an inventor, entrepreneur, or business, custom parts machining can help you bring your ideas to life, providing precision solutions for your project needs.