Crystallization processes using crystallizer tanks are widely used in various industries, including chemical, pharmaceutical, and food processing. These processes involve the separation of a substance from a solution or melt by crystallization, which is then collected and purified. While crystallization processes are essential for producing high-purity products, they can also have a significant environmental impact. In this article, we will discuss the environmental crystallizer machine of crystallization processes using crystallizer tanks and explore ways to minimize their effects.
Energy Consumption and Greenhouse Gas Emissions
Crystallization processes using crystallizer tanks require significant amounts of energy to operate. The energy is used to heat or cool the solution or melt, and to power the agitators, pumps, and other equipment. This energy consumption results in greenhouse gas emissions, which contribute to climate change. Additionally, the production of energy used in crystallization processes often involves the burning of fossil fuels, which further exacerbates the environmental impact. To minimize energy consumption and greenhouse gas emissions, manufacturers can explore alternative energy sources, such as solar or wind power, and implement energy-efficient technologies.
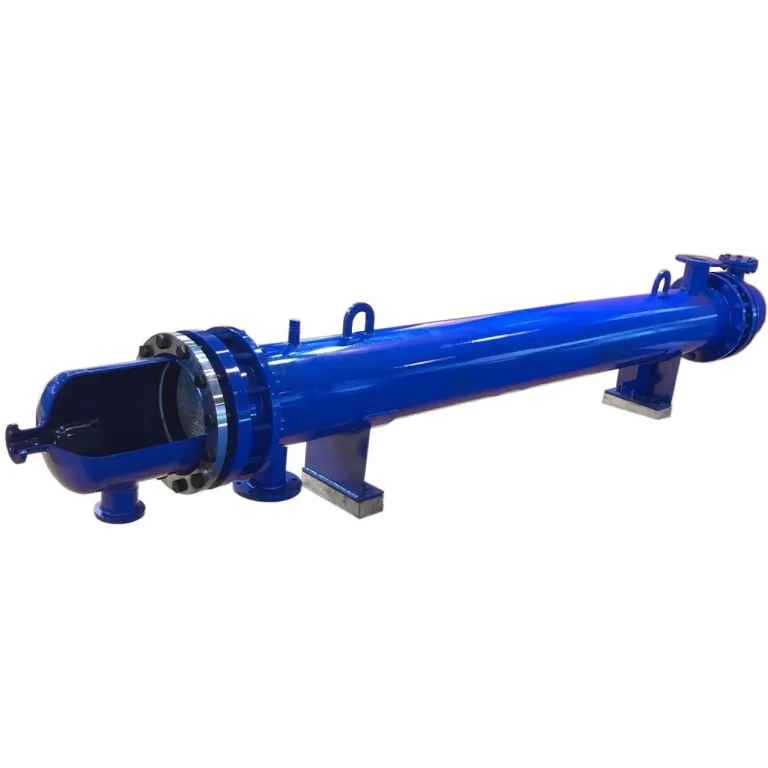
Water Usage and Wastewater Generation
Crystallization processes using crystallizer tanks often require large amounts of water for cooling, washing, and other purposes. This water usage can strain local water resources, particularly in areas where water is scarce. Furthermore, the wastewater generated by crystallization processes can contain hazardous chemicals and pollutants, which can harm aquatic ecosystems and human health. To minimize water usage and wastewater generation, manufacturers can implement water conservation measures, such as recycling and reusing water, and treating wastewater before discharge.
Chemical Usage and Disposal
Crystallization processes using crystallizer tanks often involve the use of chemicals, such as solvents, acids, and bases. These chemicals can be hazardous to human health and the environment if not handled and disposed of properly. The disposal of chemicals used in crystallization processes can also contaminate soil and groundwater, posing long-term environmental risks. To minimize chemical usage and disposal, manufacturers can explore alternative processes that use fewer or less hazardous chemicals, and implement proper chemical handling and disposal procedures.
Solid Waste Generation
Crystallization processes using crystallizer tanks can generate significant amounts of solid waste, including filter cakes, sludges, and other residues. These wastes can contain hazardous chemicals and pollutants, which can harm the environment and human health if not disposed of properly. To minimize solid waste generation, manufacturers can implement waste reduction and recycling measures, such as reusing or recycling filter cakes and sludges.
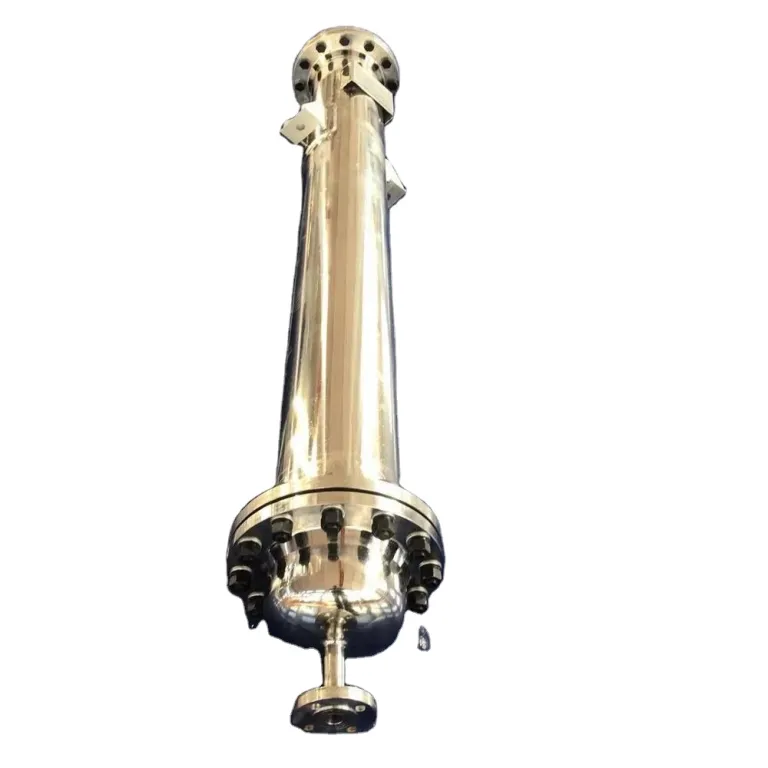
Best Practices for Minimizing Environmental Impact
To minimize the environmental impact of crystallization processes using crystallizer tanks, manufacturers can implement best practices, such as regular maintenance, process optimization, and waste reduction. Regular maintenance can help prevent equipment failure and reduce energy consumption, while process optimization can improve efficiency and reduce waste generation. Waste reduction measures, such as recycling and reusing materials, can also minimize the environmental impact of crystallization processes.
Regulatory Frameworks and Compliance
Crystallization processes using crystallizer tanks are subject to various regulatory frameworks and compliance requirements. Manufacturers must comply with environmental regulations, such as those related to air and water pollution, waste management, and chemical handling. To ensure compliance, manufacturers can implement environmental management systems, which provide a framework for managing environmental impacts and ensuring regulatory compliance.
Conclusion
In conclusion, crystallization processes using crystallizer tanks can have a significant environmental impact, including energy consumption, greenhouse gas emissions, water usage, wastewater generation, chemical usage, and solid waste generation. To minimize these impacts, manufacturers can implement best practices, such as regular maintenance, process optimization, and waste reduction, and comply with regulatory frameworks and requirements. By taking these steps, manufacturers can reduce the environmental footprint of crystallization processes and contribute to a more sustainable future.