Tapped holes are a common feature in many industrial and manufacturing applications, and play a crucial role in enhancing product assembly and durability. In this article, we will explore how tapped holes can improve product assembly and durability, and discuss the benefits of using tapped holes in various industries.
Improved Assembly
Tapped holes can significantly improve product assembly by providing a secure and reliable connection between components. By creating a threaded hole in one component and a corresponding thread on another component, tapped holes allow for easy and efficient assembly of parts. This can reduce assembly time and costs, and improve the overall quality of the final product.
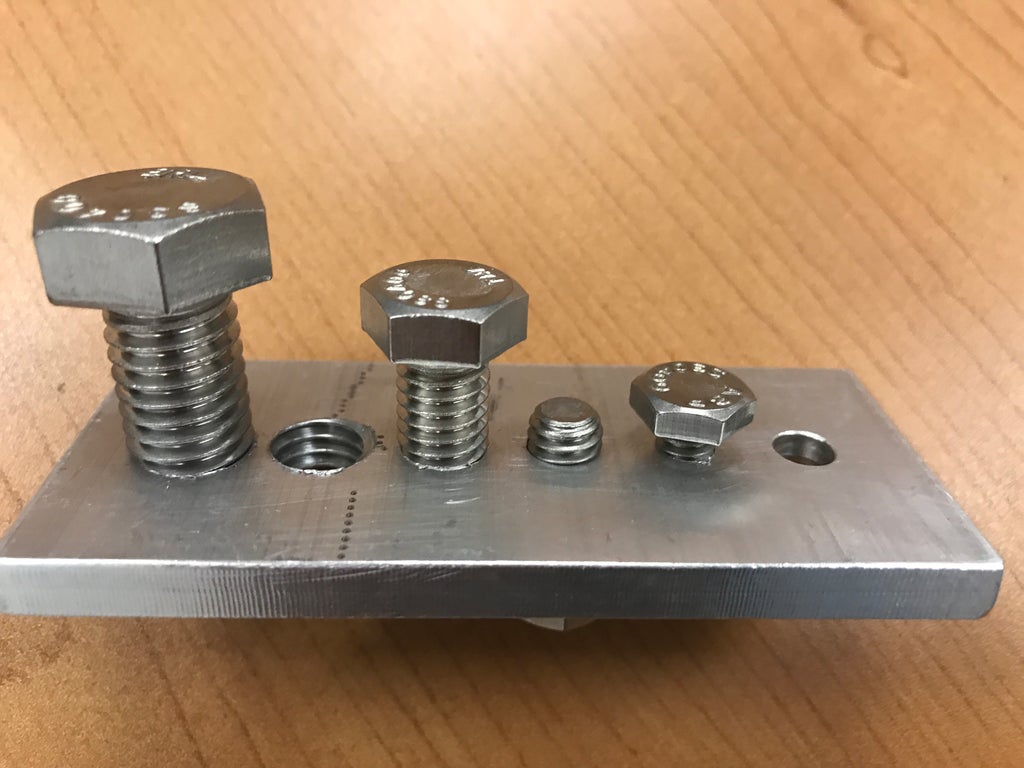
Increased Durability
Tapped holes can also increase product durability by providing a strong and secure connection between components. By creating a threaded hole in one component and a corresponding thread on another component, tapped holes can withstand high stresses and loads, and can resist vibration and fatigue. This can improve the overall lifespan of the product and reduce the need for repairs and maintenance.
Reduced Risk of Damage
Tapped holes can also reduce the risk of damage to components during assembly and use. By providing a secure and reliable connection between components, tapped hole can prevent components from becoming loose or detached, which can cause damage to surrounding components and compromise the overall integrity of the product.
Improved Safety
Tapped holes can also improve safety by providing a secure and reliable connection between components. By preventing components from becoming loose or detached, tapped holes can reduce the risk of accidents and injuries, and can improve overall product safety.
Enhanced Performance
Tapped holes can also enhance product performance by providing a secure and reliable connection between components. By creating a threaded hole in one component and a corresponding thread on another component, tapped holes can improve the overall stiffness and rigidity of the product, and can enhance its ability to withstand high stresses and loads.
Common Applications
Tapped holes are commonly used in a wide range of industries, including aerospace, automotive, construction, and manufacturing. They are used in applications such as engine mounts, gearboxes, and other machinery where high-strength connections are required.
Materials Used
Tapped holes can be created in a variety of materials, including metals, plastics, and composites. The choice of material will depend on the specific application and the required properties of the tapped hole.
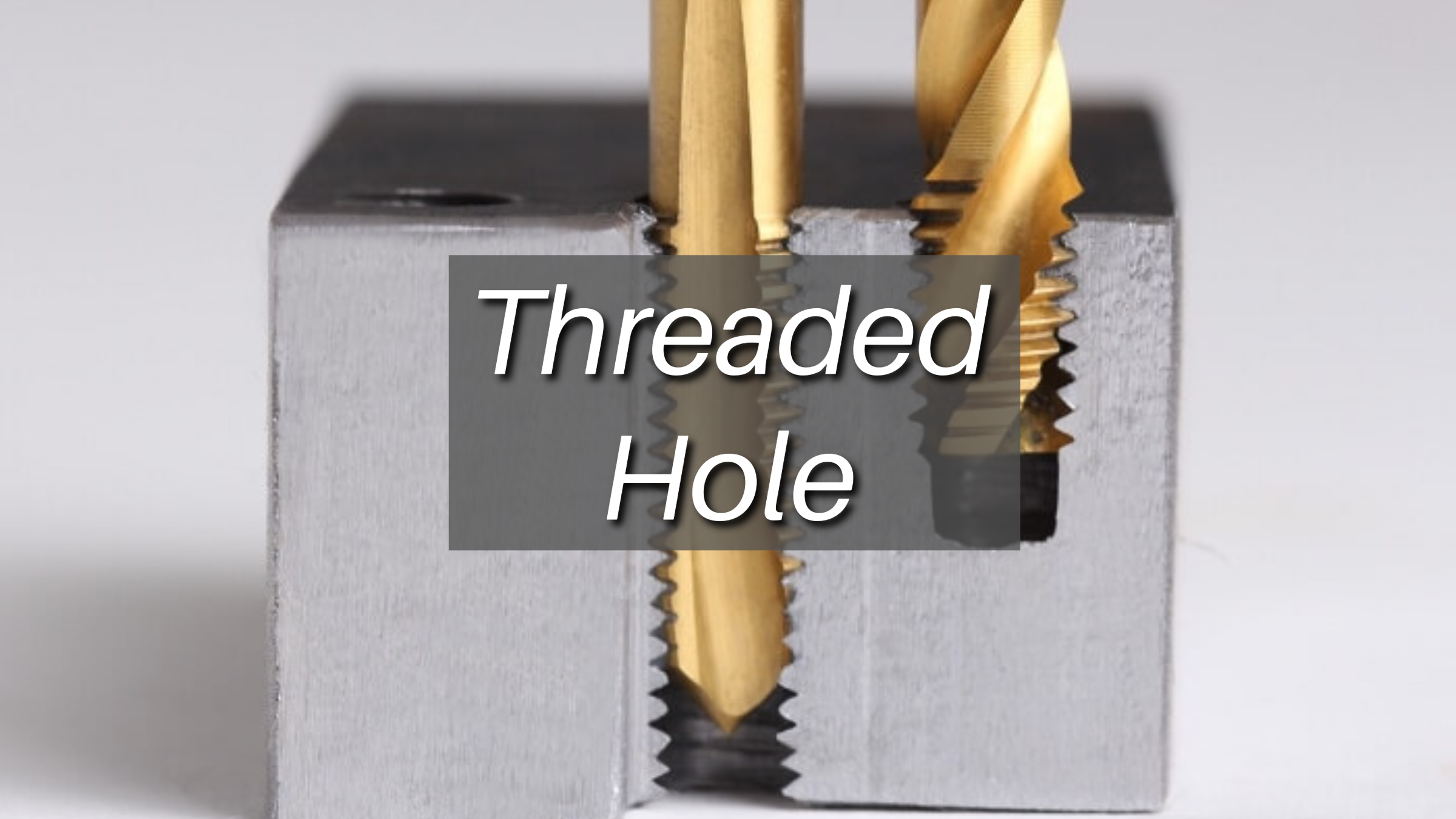
Design Considerations
When designing tapped holes, several factors must be considered, including the size and depth of the hole, the type of thread required, and the material being used. The design must also take into account any stresses or loads that will be applied to the connection.
Conclusion
In conclusion, tapped holes are a crucial feature in many industrial and manufacturing applications, and play a significant role in enhancing product assembly and durability. By providing a secure and reliable connection between components, tapped holes can improve assembly efficiency, increase product lifespan, and reduce the risk of damage and accidents. Whether you’re working on a simple manufacturing project or a complex aerospace application, tapped holes are an essential component that can provide a strong and reliable connection between components.