Die manufacturing is a complex process that involves creating a customized die that meets specific requirements and specifications. A die is a specialized tool used to cut, shape, and form materials into desired shapes and sizes. The die manufacturing process involves various techniques and technologies to produce a high-quality die. In this article, we will explore the key aspects of die manufacturing, including the techniques and technologies involved.
Die manufacturing requires a deep understanding of the material being used, the desired shape and size, and the production requirements. The process involves a combination of traditional craftsmanship and modern technologies, such as computer-aided design (CAD) software and computer numerical control (CNC) machines. The goal of die manufacturing is to produce a die that is accurate, durable, and efficient.

Material Selection and Preparation
The die manufacturing process begins with the selection and preparation of the material. The choice of material depends on the application, the type of material to be formed, and the desired lifespan of the die. Common materials used for die making process include steel, aluminum, and copper. The selected material is then cut and shaped to the required size and shape using various machining techniques, such as milling, turning, and grinding.
Machining and Fabrication
Machining and fabrication are critical stages in die manufacturing. The die material is carefully machined to achieve the required tolerances and surface finish. The fabrication process may involve additional operations, such as drilling, tapping, and welding. The die is then inspected for accuracy and quality to ensure that it meets the required specifications. Modern machining techniques, such as CNC machining and electrical discharge machining (EDM), have improved the accuracy and efficiency of the die manufacturing process.
Heat Treatment and Finishing
Heat treatment and finishing are essential stages in die manufacturing. Heat treatment involves heating the die to a specific temperature to alter its microstructure and properties. This process can enhance the die’s hardness, strength, and durability. The die is then cooled and inspected for any distortions or defects. The finishing stage involves applying a surface treatment to the die, such as polishing, coating, or plating. This enhances the die’s performance, reduces wear and tear, and improves its overall lifespan.
Die Assembly and Testing
Once the die is complete, it is assembled and tested to ensure that it functions as intended. The die is mounted on a press or other machinery, and a series of tests are conducted to verify its performance. The tests may include checking the die’s accuracy, precision, and durability. Any defects or issues are identified and addressed during this stage. The die is then certified and ready for use in production.
Technologies and Innovations
The die manufacturing process has evolved significantly over the years, driven by advances in technology and innovations. Modern die manufacturing involves the use of CAD software, CNC machines, and other technologies to improve accuracy, efficiency, and productivity. Other innovations, such as 3D printing and advanced materials, are also being explored for their potential applications in die manufacturing.
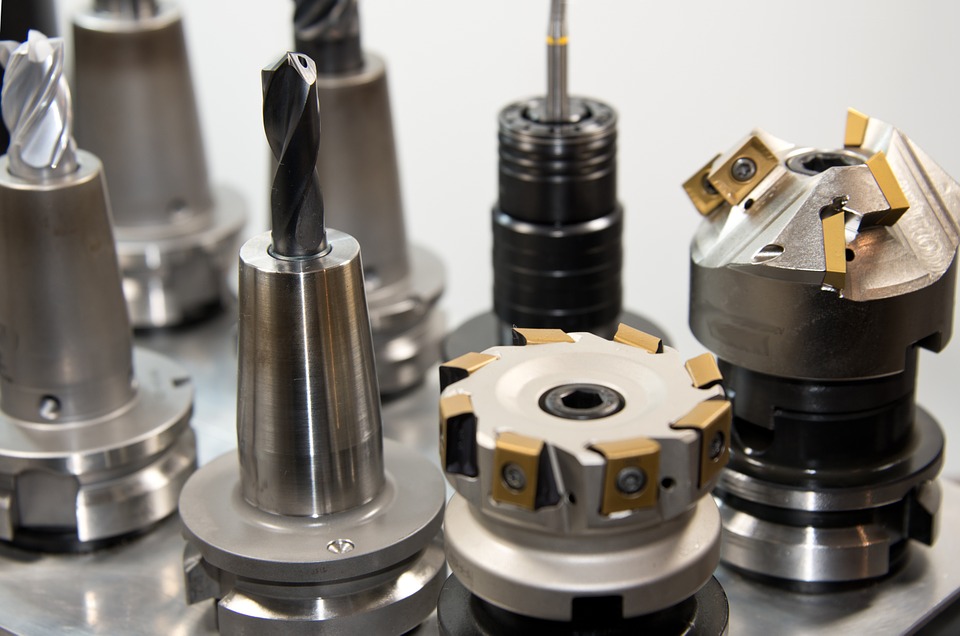
Challenges and Opportunities
Despite the advances in die manufacturing, the industry faces several challenges, including increasing competition, rising costs, and advancing technologies. The industry must adapt to new technologies and innovations to remain competitive. However, these challenges also present opportunities for growth and innovation. The increasing demand for high-precision parts and complex geometries has driven the development of new die manufacturing technologies and techniques.
Conclusion
In conclusion, die manufacturing is a complex process that involves various techniques and technologies to produce a high-quality die. The process requires a deep understanding of the material being used, the desired shape and size, and the production requirements. By leveraging modern technologies and innovations, die manufacturers can improve accuracy, efficiency, and productivity, and meet the increasing demands of modern industries.