Passion Hose is a leading manufacturer of high-quality gas hoses, committed to delivering products that meet the highest standards of quality, safety, and performance. The company’s gas hoses are designed to withstand the rigors of gas transmission and distribution, and are used in a wide range of applications. In this article, we will explore the gas hose manufacturer process behind Passion Hose’s gas hoses and what sets the company apart from other manufacturers.
Raw Material Selection and Procurement
The manufacturing process at Passion Hose begins with the selection and procurement of high-quality raw materials. The company’s gas hoses are made from a range of materials, including rubber, plastic, and metal, which are sourced from trusted suppliers around the world. Passion Hose’s procurement team works closely with suppliers to ensure that all materials meet the company’s strict quality standards.
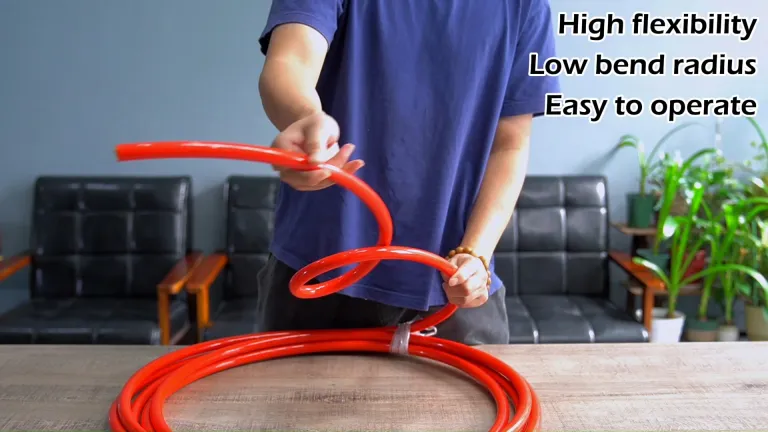
Compounding and Mixing
Once the raw materials have been procured, they are compounded and mixed to create the desired formula for the gas hose. This process involves combining the raw materials in a specific ratio to create a uniform mixture. Passion Hose’s compounding and mixing process is designed to ensure that the final product meets the required specifications and standards.
Extrusion and Vulcanization
The next step in the manufacturing process is extrusion and vulcanization. This involves heating the compounded mixture to a high temperature and then extruding it through a die to create the desired shape and size. The extruded hose is then vulcanized, which involves heating it to a high temperature to cross-link the molecules and create a strong and durable bond.
Reinforcement and Finishing
After extrusion and vulcanization, the gas hose is reinforced with a range of materials, including fabric, wire, and tape. This reinforcement provides additional strength and durability to the hose, and helps to prevent damage and wear. The final step in the manufacturing process is finishing, which involves applying a range of coatings and treatments to the hose to enhance its performance and appearance.
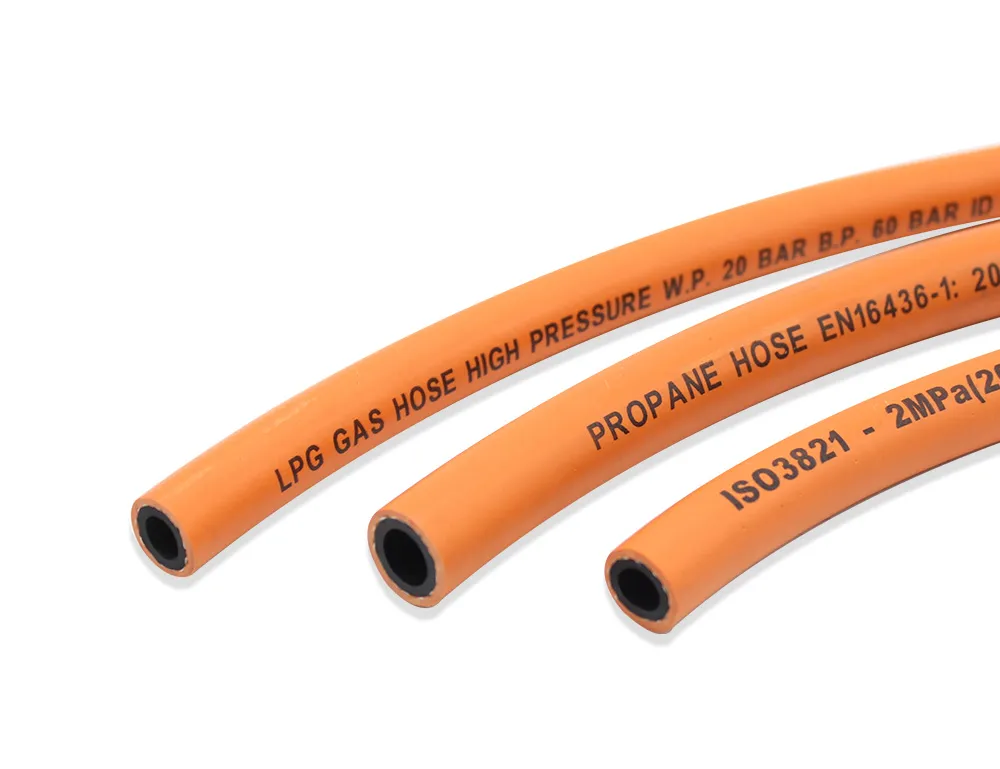
Testing and Inspection
Before the gas hose is shipped to customers, it undergoes a range of tests and inspections to ensure that it meets the required standards and specifications. Passion Hose’s testing and inspection process includes a range of tests, including pressure testing, leak testing, and durability testing. The company’s quality control team also inspects the hose for any defects or irregularities.
Certification and Compliance
Passion Hose’s gas hoses meet or exceed a range of industry standards and certifications, including ISO, SAE, and API. The company’s certification and compliance process involves working closely with regulatory bodies and industry associations to ensure that its products meet the required standards and specifications.
Conclusion
In conclusion, Passion Hose’s manufacturing process is designed to deliver high-quality gas hoses that meet the highest standards of quality, safety, and performance. The company’s commitment to using high-quality raw materials, advanced manufacturing techniques, and rigorous testing and inspection processes sets it apart from other manufacturers. With its focus on quality, safety, and customer satisfaction, Passion Hose is a trusted partner for industries around the world.