Liquid detergents are a staple in households and industries alike. The production methods for these detergents can significantly affect their quality, cost, and efficiency. Two primary methods of production are batch processing and continuous processing. Each method has its advantages and disadvantages, making the choice between them crucial for manufacturers. This article explores both methods to determine which is best for liquid detergent production line.
Understanding Batch Processing
Batch processing involves producing a specific quantity of product in a single production run. In this method, all ingredients are combined in a vessel, mixed, and processed until the batch is complete. After the batch is finished, the equipment is cleaned before starting a new batch. This method is commonly used for small to medium production volumes.
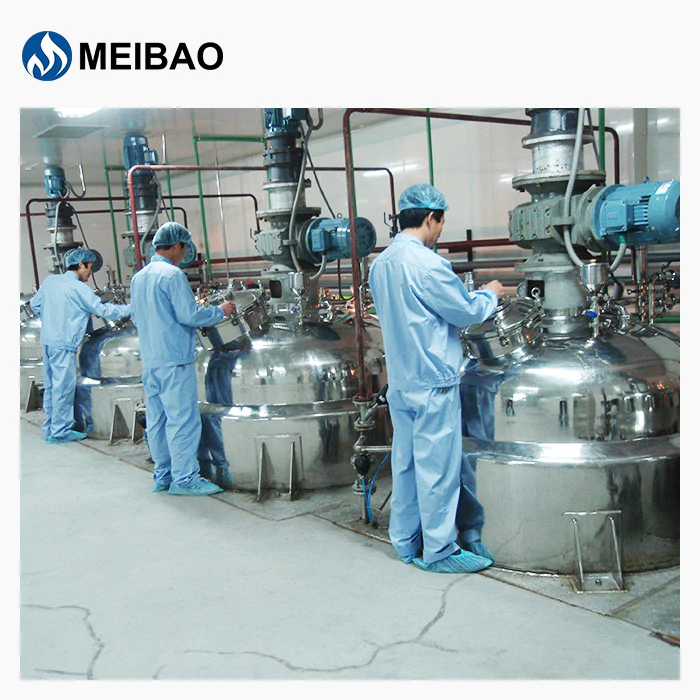
Advantages of Batch Processing
One of the main advantages of batch processing is flexibility. Manufacturers can easily change formulations or switch to different products without significant downtime. This flexibility allows for experimentation with new formulations and quick responses to market demands. Additionally, batch processing can lead to higher quality control, as each batch can be tested before moving to the next production run.
Disadvantages of Batch Processing
Despite its advantages, batch processing has some drawbacks. The cleaning process between batches can lead to increased downtime and higher labor costs. Moreover, batch processing may not be as efficient for large-scale production, as it can lead to inconsistencies between batches. This inconsistency can affect the final product’s quality and performance.
Understanding Continuous Processing
Continuous processing, on the other hand, involves a constant flow of materials through the production system. Ingredients are continuously fed into the system, and the product is simultaneously removed. This method is often used for large-scale production and can be highly efficient.
Advantages of Continuous Processing
Continuous processing offers several advantages, particularly in terms of efficiency. The constant flow of materials reduces downtime, allowing for higher production rates. This method also minimizes labor costs, as fewer operators are needed to monitor the process. Additionally, continuous processing can lead to more consistent product quality, as the process is standardized and less prone to variation.
Disadvantages of Continuous Processing
However, continuous processing is not without its challenges. The initial setup costs can be significantly higher than batch processing due to the need for specialized equipment. Additionally, changing formulations can be more complicated, requiring extensive adjustments to the system. This rigidity can make it difficult to adapt to market changes or consumer preferences.
Cost Considerations
When comparing batch and continuous processing, cost is a critical factor. Batch processing may have lower initial costs, making it more accessible for smaller manufacturers. However, continuous processing can lead to lower production costs over time due to its efficiency and reduced labor requirements. Manufacturers must carefully analyze their production volumes and market demands to determine which method is more cost-effective for their specific needs.
Quality Control
Quality control is essential in detergent production, as consumers expect consistent performance. Batch processing allows for more rigorous quality checks between batches, ensuring that any issues can be addressed immediately. In contrast, continuous processing relies on real-time monitoring to maintain quality. While both methods can achieve high-quality products, manufacturers must implement robust quality control measures regardless of the chosen method.
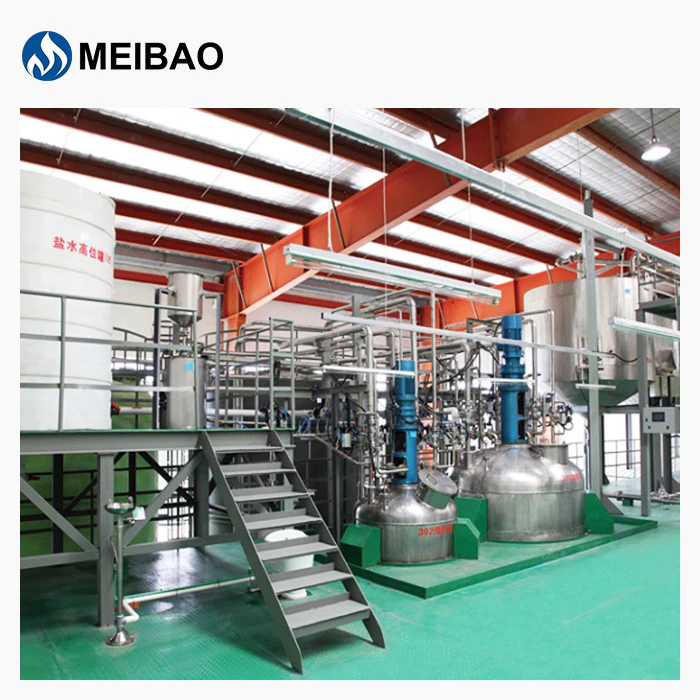
Environmental Impact
The environmental impact of production methods is becoming increasingly important for consumers and manufacturers alike. Batch processing can generate more waste due to the cleaning processes between batches. Continuous processing, while more efficient, may require more energy and resources to maintain a constant flow. Manufacturers must consider their environmental footprint when choosing a production method.
Conclusion
In conclusion, the choice between batch and continuous processing for liquid detergent production depends on various factors, including production volume, cost, flexibility, and quality control. Batch processing offers flexibility and higher quality control, making it suitable for smaller manufacturers or those producing a variety of products. Continuous processing, on the other hand, provides efficiency and consistency, making it ideal for large-scale production. Ultimately, manufacturers must weigh the pros and cons of each method to determine which is best for their specific needs.